Direct-to-garment (DTG) printing is a fantastic way for beginners to dive into the world of custom apparel printing. Unlike other printing methods, DTG printing offers a straightforward, digital process that’s perfect for small-scale productions and intricate designs.
Let’s explore direct-to-garment printers for beginners so you can make the best decisions for your direct-to-garment printing projects!
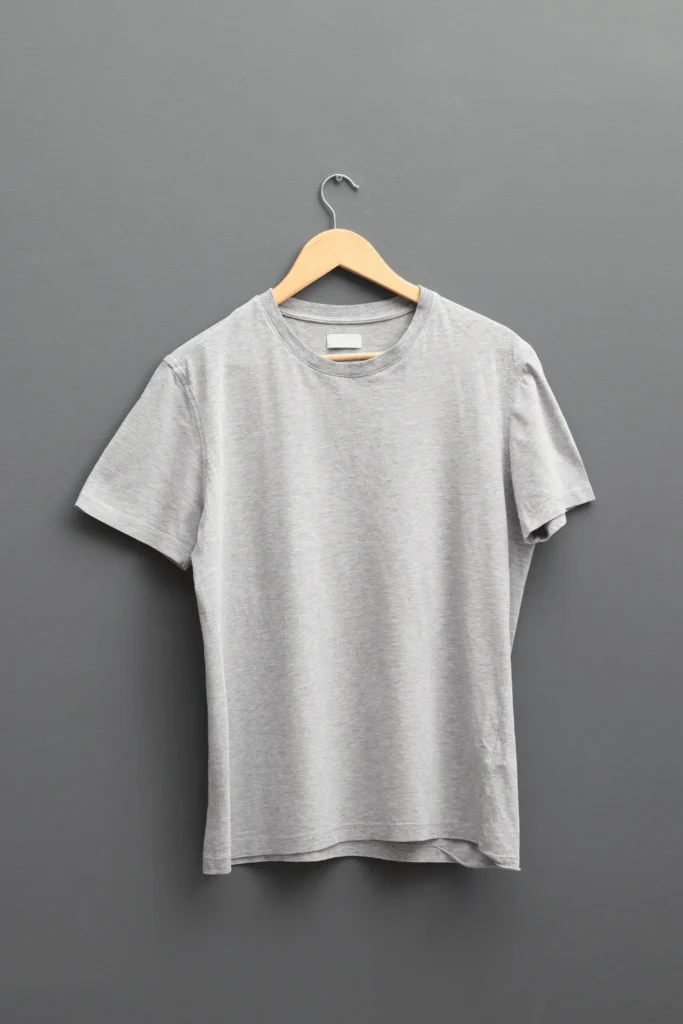
How a Direct-to-Garment Printer Works
At its core, a direct-to-garment printer operates similarly to your home inkjet printer but is designed to print on fabric instead of paper.
First, you’ll pre-treated your garment with a liquid solution that helps the ink adhere to the fabric and enhances color vibrancy.
Then, you’ll place on a platen inside the direct-to-garment printing machine. The printer then sprays water-based ink directly onto the fabric, layer by layer, to create the desired design.
Afterwards, the ink is cured using a heat press or a tunnel dryer to ensure it sets properly and becomes durable.
One of the key differences between DTG and traditional printing methods is the ease of setup. DTG printers require minimal setup time, making them ideal for printing small batches or one-off designs.
Direct-to-garment printing also allows for a broader range of colors and finer details, giving you the freedom to bring your complex designs to life!
Direct to Garment Printing vs. Screen Printing
When comparing DTG printing to screen printing, several factors come into play:
- Setup time and cost: Screen printing requires creating a stencil (screen) for each color in the design, which can be time-consuming and costly for small orders. DTG printing, on the other hand, has minimal setup time and is more cost-effective for small quantities.
- Design versatility: DTG printing excels in producing detailed, multi-colored designs with ease. It’s better to use screen printing for simpler designs with fewer colors, as each color requires a separate screen.
- Durability and feel: Screen-printed designs are known for their durability and raised texture. DTG prints are slightly less durable but offer a softer feel since the ink is integrated into the fabric.
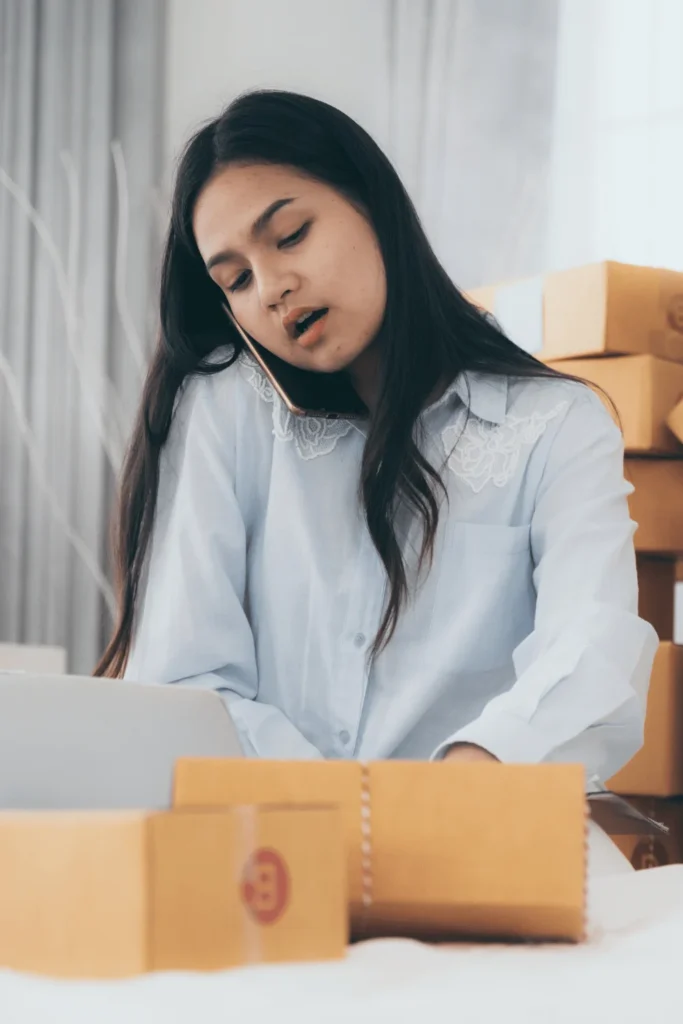
How to Use a Direct-to-Garment Printer For Beginners
As much as it’s fun to create your designs, there’s a little more you need to know to master your a direct to garment printer for beginners.
Specifically, you’ll need to understand the technical aspects that can make or break the final print. Here are some essential tips to ensure your designs are DTG-ready.
1. Choosing the Right File Format and Resolution
The resolution and format of your digital file directly affect the quality of your print. To get it right, shoot for:
- High-resolution images: Aim for a resolution of at least 300 DPI (dots per inch) to ensure your design is sharp and clear. Low-resolution images can result in blurry or pixelated prints.
- Ideal file formats: PNG and TIFF are the go-to formats for DTG printing. They support transparency and preserve the quality of your design. Avoid using compressed formats like JPEG, which can introduce artifacts and reduce image quality.
- Optimizing images: If you’re working with photographs or complex graphics, use image editing software to adjust contrast, brightness, and saturation for optimal printing results. Ensure that your design is sized correctly for the garment and positioned where you want it to appear.
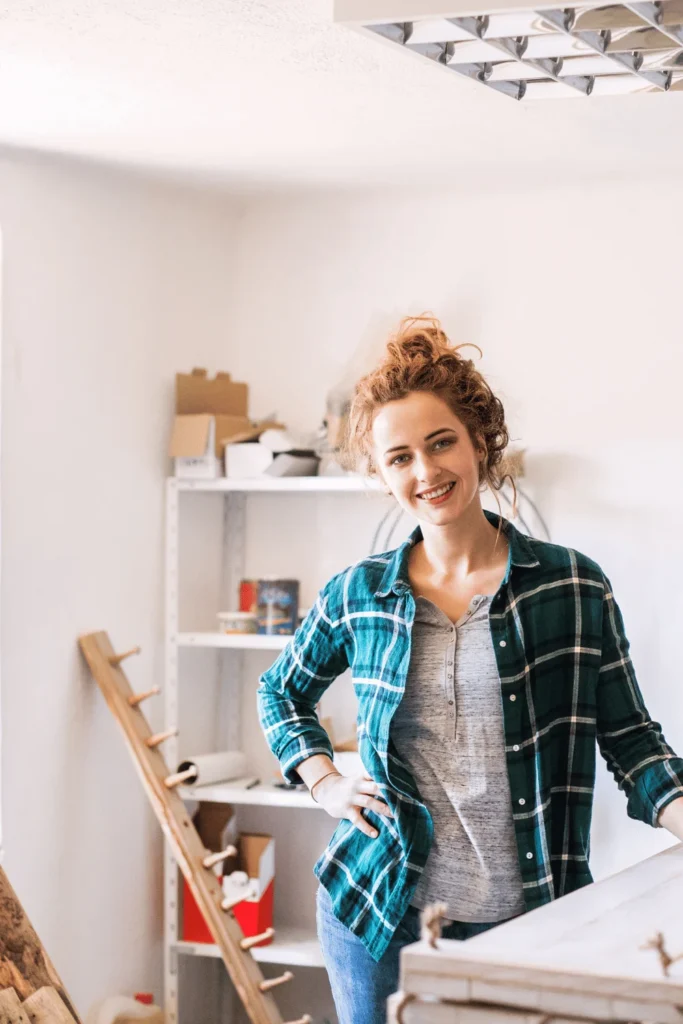
2. Color Management and Matching
Color accuracy is crucial in direct-to-garment printing for beginners; it all starts with proper color management:
- Color profiles: Use color profiles (such as Adobe RGB or sRGB) to ensure consistent color reproduction from your screen to the printer. This helps maintain the integrity of your original design colors.
- Matching screen colors to printed colors: Be aware that colors may appear differently on various screens and might not translate exactly onto the fabric. Test print your design on a sample garment to check how the colors render in real life.
- Calibrating monitors and printers: Regularly calibrate your monitor and printer to maintain color accuracy. This ensures that the colors you see on your screen are as close as possible to the colors that get printed.
3. Understanding the Limitations of DTG Printing
While DTG printing offers great flexibility, be aware of its limitations, one of which is printing on dark fabrics.
The printer uses white ink as a base layer when printing on dark fabrics, which can affect the vibrancy of your colors.
Getting a bright white print can also be challenging, especially on darker fabrics. Consider the fabric color and adjust your design accordingly to ensure the whites stand out.
Overall, keep in mind that some designs might need modification to suit the unique DTG printing process.
4. RIP Software
RIP (Raster Image Processor) software plays an important role in the world of DTG printers.
This specialized software bridges between your design and the printer, ensuring that your artwork is translated accurately onto the fabric.
RIP software converts your digital design into a format that the DTG printer can understand, optimizing the image for printing. It controls the amount and placement of ink, manages colors, and can even adjust for the type of fabric you’re printing on.
With advanced color management tools, RIP software will make sure your printer reproduces your design faithfully on the garment. It can also enhance details and gradients and result in a higher-quality print.
Make sure to look out for DTG printers that come with their own RIP software, as not all of them do. All Ricoma printers have RIP software included as part of our all-inclusive DTG printer bundle as per our vision.
5. Proper Maintenance and Cleaning
Maintaining your direct-to-garment printer is crucial for its longevity and the quality of your prints. Regular maintenance can prevent common issues like clogs and ensure that your printer runs smoothly.
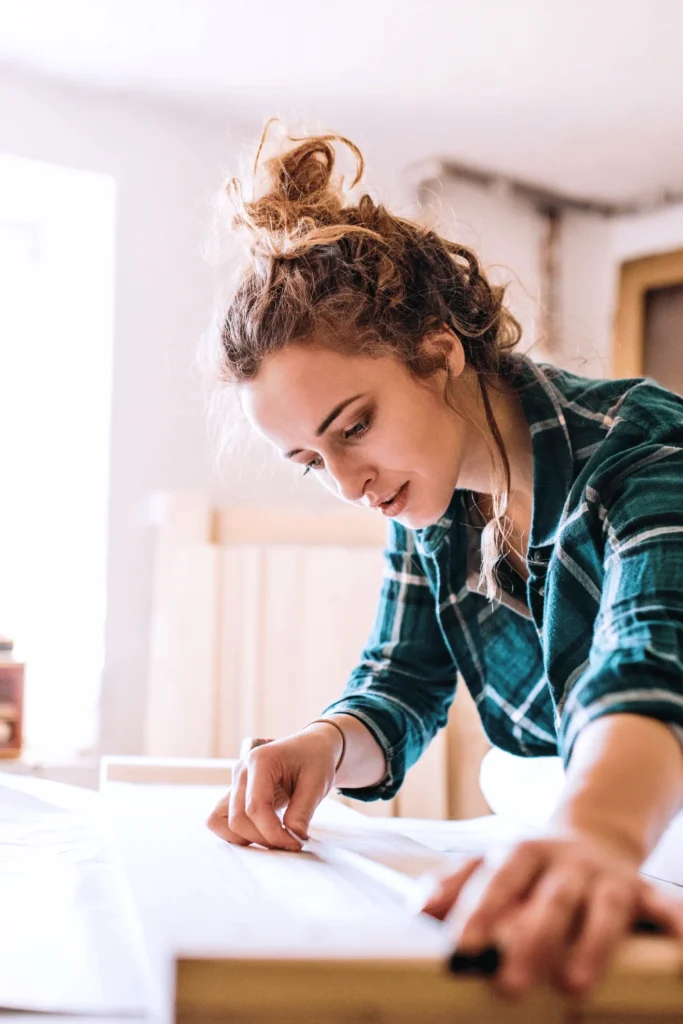
Here’s a quick basic maintenance checklist:
- Daily tasks
- Nozzle check
- Head cleaning cycle to prevent ink clogs
- Wipe down the platen and surrounding areas to remove any ink residue or debris
- Weekly tasks
- Check and clean the encoder strip
- Inspect the ink lines and dampers for any signs of ink buildup or leaks
- Monthly tasks
- Deep clean the print head and cap station
- Check for any firmware updates
- Ensure that your RIP software is up to date
6. Avoiding Common Printing Mistakes
Even with the best equipment, mistakes can happen.
Applying too much or too little pretreatment can affect print quality. Follow the manufacturer’s guidelines and adjust based on the fabric type and color.
You’ll also want to make sure that your prints are fully cured, whether you’re using a heat press or a tunnel dryer. Under-cured prints can lead to fading or wash-out.
And above all, always test your prints on a sample garment before starting a production run!
Use these tests to refine your settings and learn from any mistakes.
7. Understanding Fabric Compatibility
Not all fabrics are created equal when it comes to direct-to-garment printing.
The type of fabric you choose can significantly impact the final print quality.
Cotton is one of the best fabrics for DTG printing because of its smooth surface and ability to absorb ink well.
Blends with a high cotton content also work well, but the higher the synthetic content, the less vibrant the print may be.
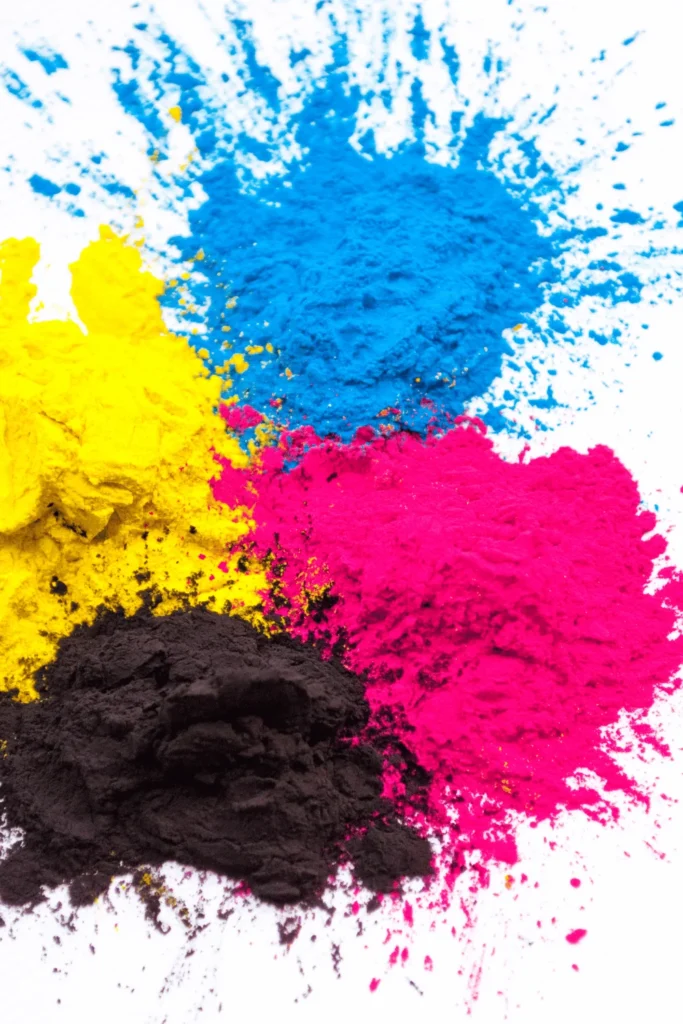
The tighter the weave of the fabric, the smoother the surface, which can lead to sharper prints. But fabrics with a looser weave or more texture, like linen or slub cotton will create a more vintage or distressed look.
For bright and detailed prints for your direct to garment printer for beginners, go for high-quality, tightly woven cotton. For a more relaxed or vintage look, experiment with different textures and blends.
Explore Ricoma’s DTG Printers for a Seamless Printing Business!
Our Ricoma printers and supplies help creative entrepreneurs and small business owners streamline their creation process. Learn from our YouTube channel, find your next favorite tool, and find the best direct to garment printer for beginners!