When it comes to the best DTF ink, the ink you pick can make or break your final product, affecting everything from color vibrancy to durability. But with so many options on the market, how do you know what to look for?
First and foremost, it’s essential to understand that not all inks are created equal with DTF printing!
The quality of your direct-to-film printing directly impacts the overall printing process and the appearance of your finished product.
High-quality DTF printer ink will produce vibrant, accurate colors that resist fading and cracking, even after multiple washes. On the other hand, lower-quality inks may result in dull, inconsistent colors that quickly fade or peel.
Understanding the DTF Transfer Process: Composition, Differentiators
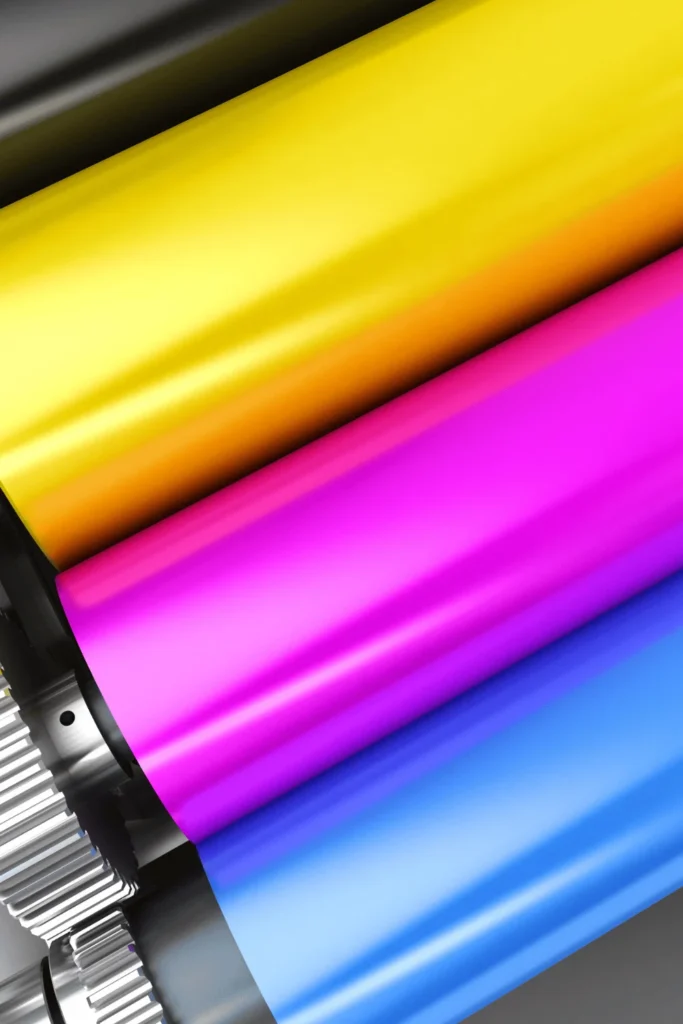
Before we delve into the specifics of choosing DTF ink, it’s important to understand what sets it apart from other types of printing inks.
DTF ink is a specialized formulation designed specifically for the Direct-to-Film printing process. Unlike traditional screen printing inks or direct-to-garment (DTG) inks, DTF ink is engineered to adhere to a special film before being transferred to the final fabric.
The chemical composition of DTF powder adhesive is unique, typically consisting of pigments, binders, and additives that work together to create a durable, flexible print.
These inks are water-based, which makes them eco-friendly and easy to work with. The DTF ink pigments provide the color, while the binders ensure the ink adheres properly to both the film and the fabric. Additives are included to enhance properties like flow, durability, and washfastness.
One of the main advantages of DTF vs. screen printing is its versatility. DTF prints can be applied to a wide range of fabrics, including cotton, polyester, blends, and even challenging materials like nylon and leather.
This flexibility in fabric printing is a game-changer for businesses looking to expand their product offerings without investing in multiple printing technologies.
Another key differentiator is the ability of DTF ink to produce vivid, full-color designs on dark fabrics without the need for pretreatment. This is possible thanks to the unique white ink base layer used in the DTF process, which we’ll discuss in more detail later.
The specific characteristics that make DTF ink suitable for fabric printing include its excellent opacity, flexibility, and ability to withstand repeated washing and wearing. These inks are designed to stretch with the fabric without cracking or peeling, ensuring your prints look great wash after wash.
Key Factors to Consider When Choosing DTF Ink
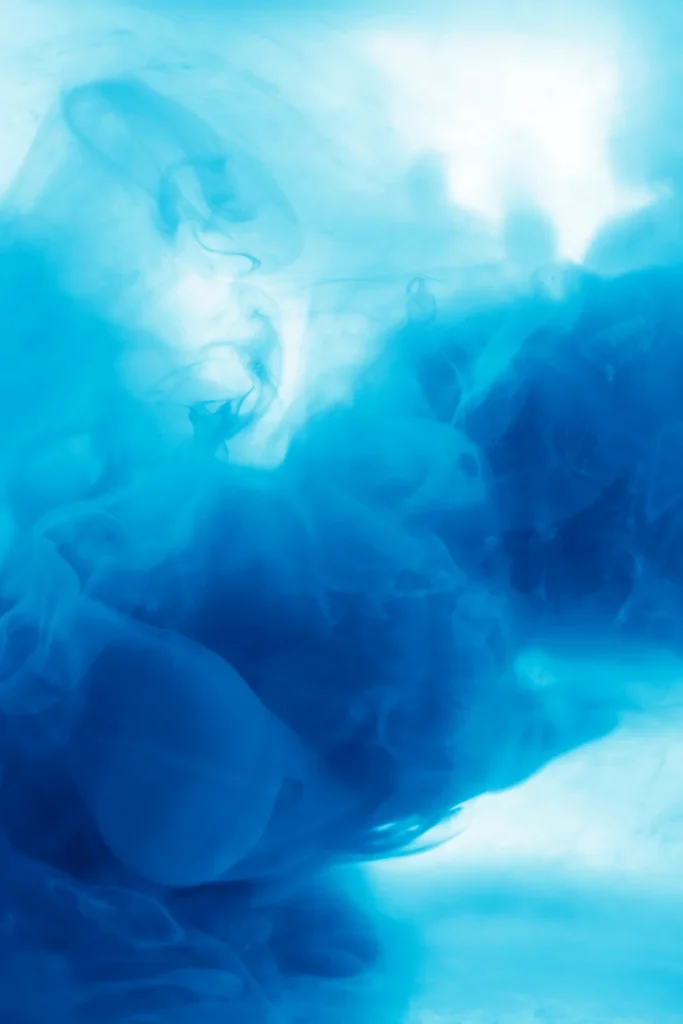
Color Vibrancy and Accuracy
Vibrant colors catch the eye and make your designs pop, which is especially crucial in the competitive world of custom apparel and accessories. When evaluating DTF inks, look for options that offer rich, saturated colors that maintain their intensity even after being transferred to the fabric.
Color accuracy is equally important, especially if you’re printing designs with specific brand colors or trying to match existing products.
Durability and Washfastness
Washfastness refers to the ability of the print to maintain its color and integrity after repeated washing. Durable prints resist cracking, peeling, and fading, ensuring customer satisfaction and reducing returns or complaints.
Several factors affect the durability of DTF prints, including the quality of the ink, the curing process, and the type of fabric being printed on. High-quality DTF ink durability is formulated to bond strongly with the fabric fibers, creating a print that becomes part of the garment rather than sitting on top of it.
Ink Viscosity and Flow
Viscosity refers to the thickness or flowability of the ink, while flow describes how easily the ink moves through the printer and onto the film.
The right viscosity is essential for achieving clean, crisp prints. If the ink is too thick, it may clog print heads or result in poor detail reproduction. Conversely, if it’s too thin, it may spread too much on the film, leading to blurry or fuzzy prints.
Drying and Curing Time
The DTF ink curing process is a critical step in DTF printing that affects both the quality of your prints and your production efficiency. Drying refers to the evaporation of water from the ink, while curing involves the chemical bonding of the ink to the fabric.
DTF inks typically require a two-step process: first, the ink is dried on the film, and then it’s heat-pressed onto the fabric where it undergoes final curing. The time required for each step can vary depending on the ink formulation and your equipment.
Compatibility with DTF Printers and Films
Compatibility between your ink, printer, and film is crucial for achieving high-quality DTF prints. Using incompatible components can lead to poor print quality, clogged print heads, and wasted materials.
And while it may be tempting to mix and match components from different manufacturers to save costs, doing so can lead to inconsistent results and potential equipment damage.
Types of DTF Ink
DTF ink generally fall into three main categories: white ink, CMYK inks, and specialty inks. Each type plays a crucial role in the DTF printing process and offers unique benefits for different applications. Let’s take a closer look at each category.
White DTF Ink
White ink is arguably the most important component in DTF printing, especially when working with dark fabrics. It serves as a base layer that allows vibrant colors to pop on dark backgrounds, much like a primer does in painting.
The unique properties of white DTF ink include high opacity and excellent coverage. A good white ink should provide a smooth, even base that completely covers the underlying fabric color without appearing chalky or textured.
CMYK DTF Inks
CMYK (Cyan, Magenta, Yellow, and Key/Black) inks are the foundation of full-color printing in DTF systems. This color model allows for the creation of a wide range of colors by mixing these four base colors in various proportions.
The benefits of using CMYK inks for full-color prints include the ability to reproduce photorealistic images and achieve a broad spectrum of colors. CMYK printing is also generally more cost-effective than using individual spot colors for multi-color designs.
Specialty DTF Inks
Specialty DTF ink opens up a world of creative possibilities beyond standard CMYK colors. These can include metallic inks, fluorescent colors, and even clear inks for special effects.
Metallic inks can add a luxurious, eye-catching element to your designs, perfect for logos or accent details. Fluorescent inks create vibrant, attention-grabbing prints that seem to glow under certain lighting conditions. Clear inks can be used for subtle effects or to add a glossy finish to specific areas of your design.
When working with specialty inks, be aware that they may require different handling and printing techniques compared to standard CMYK inks. For example, metallic inks may need more frequent stirring to prevent settling, while fluorescent inks might require additional curing time to achieve maximum vibrancy.
Make the Best Choices for Your DTF Printing with Ricoma!
When it comes to DTF printing, choosing the right ink is just one piece of the puzzle. To truly excel in this printing method, you’ll need a machine that can create the best results time and time again. Explore our Revel 1202 and Revel 2402 to help you create cutting-edge and unique designs!